摘要
探讨棉纺赛络纺纺纱工艺。分析论述了棉纺赛络纱的特点及赛络纺改善成纱强力、条干和毛羽的工艺原理,对赛络纺粗纱定量、粗纱捻系数、细纱罗拉隔距,喇叭口中心距、后区牵伸倍数、钳口隔距、导纱动程、细纱捻系数及钢领钢丝圈、胶辊选用、络筒速度、清纱门限等进行了试验分析。指出:通过合理配置工艺参数及纺纱专件,能够充分发挥赛络纺的优点,实现强力高、毛羽少、条干好的纺纱效果。
1.棉纺赛络纺的特点
棉纺赛络纺纱是一种平行喂入双根粗纱,输出后并合加捻的新型纺纱技术。赛络纺纱成纱结构特殊,表面呈单纱形态,截面呈圆形,表面纤维排列整齐顺直,毛羽少,抗耐磨性能好,具有股线的特点,而同股线相比又不易分成单纱。棉纺赛络纱强力高,条干好,毛羽较少,用赛络纺纱织成的织物表面清晰,硬挺度好,有骨质感但又不失柔软性能,布面毛羽少,因而受到用户的青睐。
2.棉纺赛络纺纱的工艺原理
赛络纺是将两根保持一定间距的粗纱平行地喂入细纱机,经牵伸后由前罗拉输出两根单纱须条。这两根单纱须条再汇合成一根单纱同向加捻,形成一个加捻三角区,合并加捻后卷绕到纱管上,锭子和钢丝圈同向回转给纱线加上一定的捻度,捻度自上而下传递至前罗拉握持处,在汇集点上的两根单纱分为两个捻向相同、作用力相向的一对三角区,从而形成3个三角区相互作用,连续输出纱线。由于单纱加捻区较短,单纱中纤维螺旋角较小,捻幅也较小,仅从单纱来分析,其强力较小,纤维两头外伸也较少,同向加捻后捻幅在原有单纱捻度的基础上迅速增加,抱合力提高,毛羽减少,强力增加明显。棉纺赛络纺纱有类似于股线的结构和风格,在与单纱使用同样的原料,相同比例和捻度的情况下,其成纱强伸性能优于单纱。
传统纺纱中单纱上的表面纤维和毛羽仍在纱线表面,在后加工时经过强烈的摩擦增加新的毛羽。赛络纺纱两根被牵伸后的须条在加捻过程中,单根须条加上少许捻度后,再相互为中心加捻并合为一根赛络纱,将单根须条上的毛羽包卷进纱线中,进而改善成纱毛羽。同时由于须条捻向相同,改善了单纱的扁平结构,形成了横截面呈圆形的独特结构,在络筒退绕时减少摩擦,毛羽增长也较少。
赛络纺纱因为两根粗纱同时被牵伸起到一定的并合作用,两根须条相互弥补,对改善粗节、细节、条干有一定的作用。但是对条干的弥补有一定的限制,条干的改善取决于须条喂入喇叭口中心距的大小。过小赛络纺纱效果不明显,条干恶化;过大两根须条间的夹角过大,单纱须条张力变化大,捻度上传极限高度汇聚点的捻合力突变,张力不稳定,成纱中两须条纤维张力不一致,承受外力的一致性差,纤维排列不一致影响条干的均匀度,因此在保证条干时必须兼顾喂入喇叭口的中心距工艺。
3.棉纺赛络纺纱主要工艺选择
3.1 粗纱定量的选择
赛络纺纱工艺中,粗纱的喂入定量与成纱质量有密切联系。粗纱定量应根据所纺纱线线密度而定,同时又要兼顾牵伸倍数增大造成的牵伸附加不匀这一负面影响。在选用时,纺18.2tex以上的细号纱线时,粗纱定量应比原粗纱定量的50%再偏小0.3g/10m~0.5g/10m掌握,有利于成纱质量的稳定;纺制18.2tex以下的低特纱线时,应比原粗纱定量50%再偏小0.8g/10m~1.5g/10m掌握,便于减少牵伸带来的不匀。
3.2 粗纱捻系数的确定
粗纱捻系数大小与牵伸力大小呈正相关。棉纺赛络纺选用粗纱捻系数,在不改变其他工艺的前提下牵伸力已明显增加,如不调整则会出现牵伸不开的问题。当喂入纱条呈双纱喂入时,牵伸力发生改变,其加压控制力以及罗拉的隔距都发生改变。在增大后区隔距的情况下,选用粗纱捻系数较正常捻系数偏大掌握,便于细纱捻回重分布的利用。58.3tex赛络纱粗纱捻系数对成纱质量的影响试验结果如下:
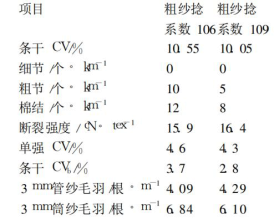
由试验数据可以看出,粗纱捻系数增加对赛络纺纱较为有利,原因是捻系数大,纤维间残存的捻度大,纤维的捻度损失小,有利于纤维的排列,纱线对表面纤维的圈结能力进一步增强,对成纱质量有一定的改善作用。
3.3 细纱主要工艺
3.3.1 后区隔距及牵伸倍数的选择
细纱后区工艺包括后区牵伸倍数和后区隔距。棉纺赛络纺纱双纱喂入,牵伸力增大,后区工艺必须进行相应的调整。后区工艺的原则是大隔距、小牵伸。
后区牵伸倍数大,捻回重分布大,捻度损失大,后区牵伸倍数小,捻回重分布小,捻度损失小,纤维排列稳定有利于成纱质量的提高。同时为了利用捻回重分布后区隔距偏大掌握,一般为18mm×35mm,以利于提高成纱质量。58.3tex纱后区牵伸倍数对成纱质量的影响试验结果见表1。

由试验数据可知,选用1.20倍的后区牵伸倍数,可以获得较好的纺纱效果。
3.3.2 喂入喇叭口中心距的优选
喂入喇叭口中心距是赛络纺纱的重要工艺之一。喂入粗纱喇叭口间距决定粗纱间距。粗纱间距指经过牵伸的两根纱条在离开罗拉钳口时的距离。间距大,须条间的夹角过大,单纱须条过长,张力变大,须条三角区缩小,边纤维损失多,毛羽减少,但是在加捻三角区中边纤维损失反而影响成纱质量。间距小夹角小,须条短,张力小,毛羽较稳定,成纱质量也较为稳定,但不宜过小,过小变成双纱喂入,赛络纺的风格无法体现,一般喇叭口的中心距在5mm左右。29.8tex赛络纱喂入喇叭口中心距优选试验结果见表2。
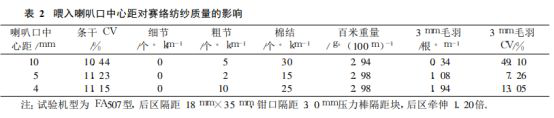
从表中数据可以看出,喇叭口的中心距选用10mm时,条干虽好,但棉结和粗节较多;同时由于边纤维卷取受力三角区变形,纤维损失过多造成百米重量较轻。此外反映毛羽段与段差异的3mm管纱毛羽CV值49.1%,证明毛羽段与段之间的差异太大;选用4mm时容易出现两根粗纱交叉,赛络纺纱的风格无法体现,并且粗节、棉结也较多。因此选用5mm的中心距,能够体现出质量改善和降低毛羽的优势。
3.3.3 捻系数的确定
细纱工序要在减少毛羽的同时,尽可能的少产生疵点。针织用纱的捻系数宜偏小掌握,但根据赛络纱的成纱机理,为了减少毛羽,防止纤维在单纱须条中滑移,选取比同号数普通环锭纺纱偏大的捻系数,一般针织纱设计为340~350,机织纱设计为370~380。
3.3.4 钢领、钢丝圈的选用
赛络纺纱线毛羽少,结构紧密,超低的毛羽导致了钢领和钢丝圈动摩擦的润滑不足,钢丝圈在钢领的回转面上阻力增大,钢领和钢丝圈的接触区域将产生高温,使钢领钢丝圈过早磨损。同时加大纺纱段的张力,造成输出钳口三角区的不稳定,从而导致钢丝圈运行不稳定、纱线张力波动和纱线质量降低。所以必须配置与此相适应的钢领、钢丝圈,否则会造成大量断头。一般钢领选用PG1-4254或PG1/2-3854,钢丝圈一般选用6903系列,其圈形为矩形并开“天窗”便于散热。
3.3.5 细纱导纱动程的确定
赛络纺纱由于存在3个小三角区,导纱动程使须条移动容易产生三角区的波动,造成单纱断头的现象多,在毛纺一般不用。导纱动程主要为保护胶辊、延长胶辊的使用寿命。棉纺赛络纺纱可以根据须条的中心距进行确定,胶辊宽度在30mm,选用10mm的导纱动程容易造成边纤维在胶辊边缘散失或造成纱疵。导纱动程偏小掌握,一般在4mm~6mm。
3.3.6 钳口隔距的确定
细纱钳口决定须条和纤维运动牵伸力稳定与否。钳口隔距应根据纺纱线密度、胶圈厚度和弹性、上销弹簧的压力、纤维的长度及其摩擦性能和前罗拉加压条件参数予以确定。在赛络纺纱中,喂入须条的增加,牵伸力相应增大,钳口隔距偏小掌握对质量有利,一般以不出“硬头”为原则,纺相同号数纱线时相对于传统环锭纺钳口隔距应减少0.25mm~0.50mm为宜。
3.3.7胶辊及工艺压力的确定
胶辊是纺纱的重要牵伸部件,对成纱质量有直接影响,要求胶辊表面对纤维束有足够握持能力,且不发生缠绕现象。赛络纺纱线结构紧密,牵伸力大,须条横动动程短,胶辊产生中凹磨损较快。为减少胶辊磨损对纱线质量的影响,应用表面不处理胶辊,铁芯与胶管内表面均匀接触。前胶辊3个月~4个月磨砺一次。磨砺时采用慢行程、小磨量,使胶辊处于均匀受力状态。工艺压力同传统纺纱相比偏重掌握,胶辊直径偏大选择,一般前中后双锭压力为140N×120N×140N,胶辊直径在29.0mm~30.0mm之间。
3.4 络筒有关工艺选择
3.4.1 清纱工艺的设置
络筒工序主要的任务是清除有害纱疵,防止成纱指标恶化。络筒工序采用低速度、小张力、严格清纱门限的工艺原则。赛络纺纱在络筒工序中毛羽的增长幅度较常规纺纱方法明显减少,主要清除细纱工序单根粗纱纺纱造成的长细节。电清门限严格控制,具体工艺参数为:棉结400%;短粗节300%×1.5cm;长粗节25%×20cm;长细节-30%×9cm。
3.4.2 络筒速度的选择
采用较低的速度和适宜的张力,防止条干恶化及棉结增加,要求络纱通道光滑,采用空气捻接器,络纱速度根据所纺纱线进行设计,自动络筒比相同纱号低100m/min~200m/min;槽筒速度比相同纱号低50m/min~100m/min;张力工艺根据所纺线密度偏小掌握。
4 结语
(1)棉纺赛络纺纱是一种平行喂入双根粗纱,输出后并合的新型纺纱技术,其成纱风格具有股线的效果。棉纺赛络纺纱改善质量的原理是纺纱特性所决定的。在纺纱工艺中3个加捻三角区相互作用、同向加捻,从而减少了毛羽,提高了强力,改善了条干。
(2)棉纺赛络纺纱的主要工艺:粗纱采用大捻系数,定量偏轻控制;细纱以“一重两大三小二适中”为原则,即重加压,大后区隔距、大胶辊直径,小后区牵伸倍数、小钳口隔距、小导纱动程,钢领钢丝圈适中、喇叭口中心距适中;络筒低车速、小张力,严清纱。
(3)通过实践证明棉纺赛络纺纱流程中,在粗纱、细纱、络筒采用有效的工艺措施,能够充分发挥赛络纺的优点,实现强力高、毛羽少、条干好的纺纱效果。
(本网尊重各兄弟网站及独立撰稿人之版权,如发现本网刊登您的稿件而未署名,请联系我们.同时本网也欢迎对市场具有敏锐判断和独立见解的行业人士前来投稿,投稿邮箱info@168tex.com
电话:0512-63082910)